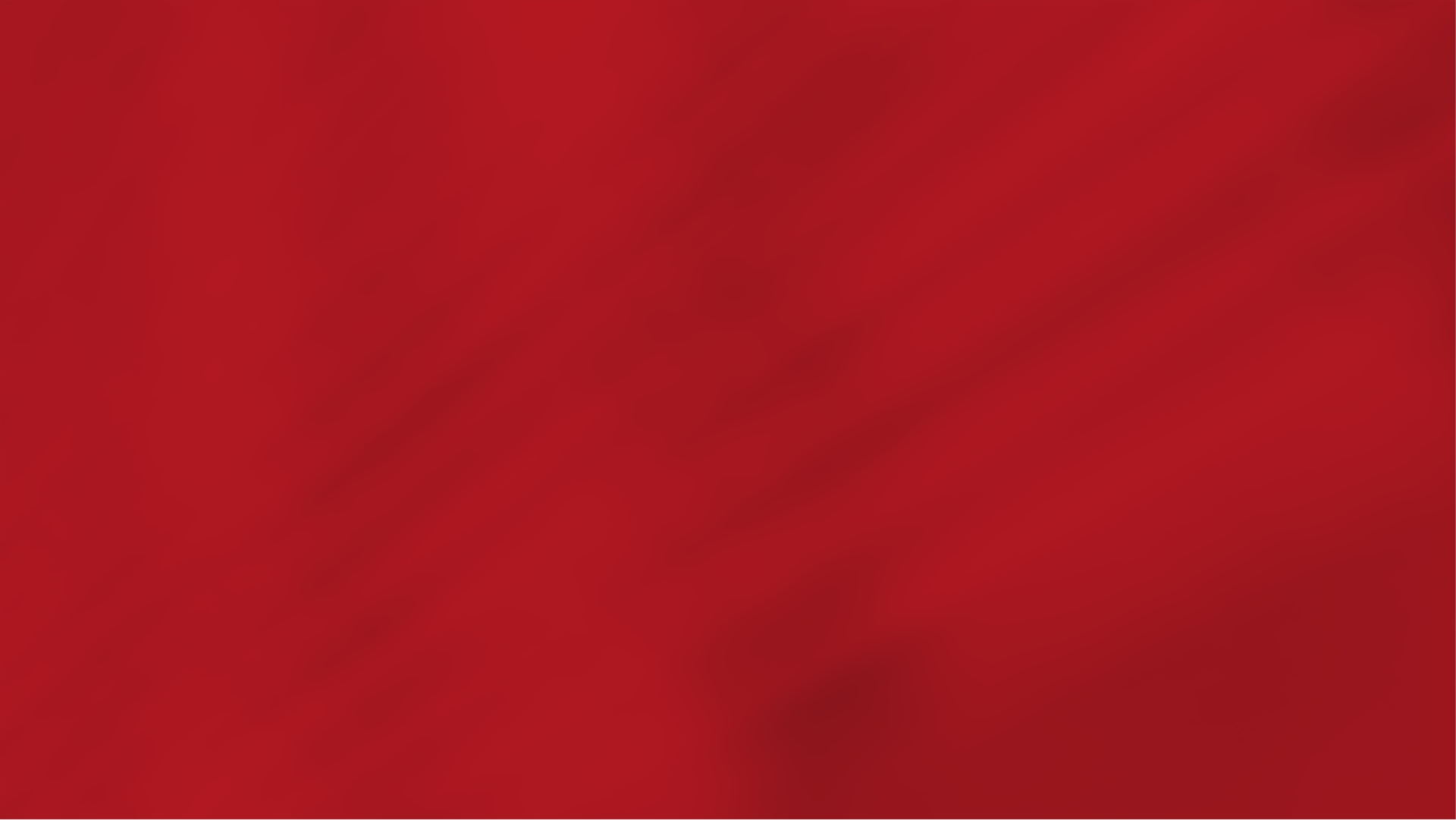
Aero FlightSystems
Aero FlightSystems in Texas produce parts for Boeing's aircraft factories. The aircraft components are large and heavy, and handling e.g. the nose of the aircraft has so far required a team of eight people.
A need for handling large, unmanageable components
Employees often experienced sore shoulders and backs, as the job involved many heavy and difficult lifts throughout a workday. The large aircraft components must be moved through several workstations in the factory, and the many irregular shapes of the components mean that a traditional forklift cannot be used – thus, manual lifting was necessary.
This increases the risk of acute work injuries and leads to physical strain and wear on the employees.
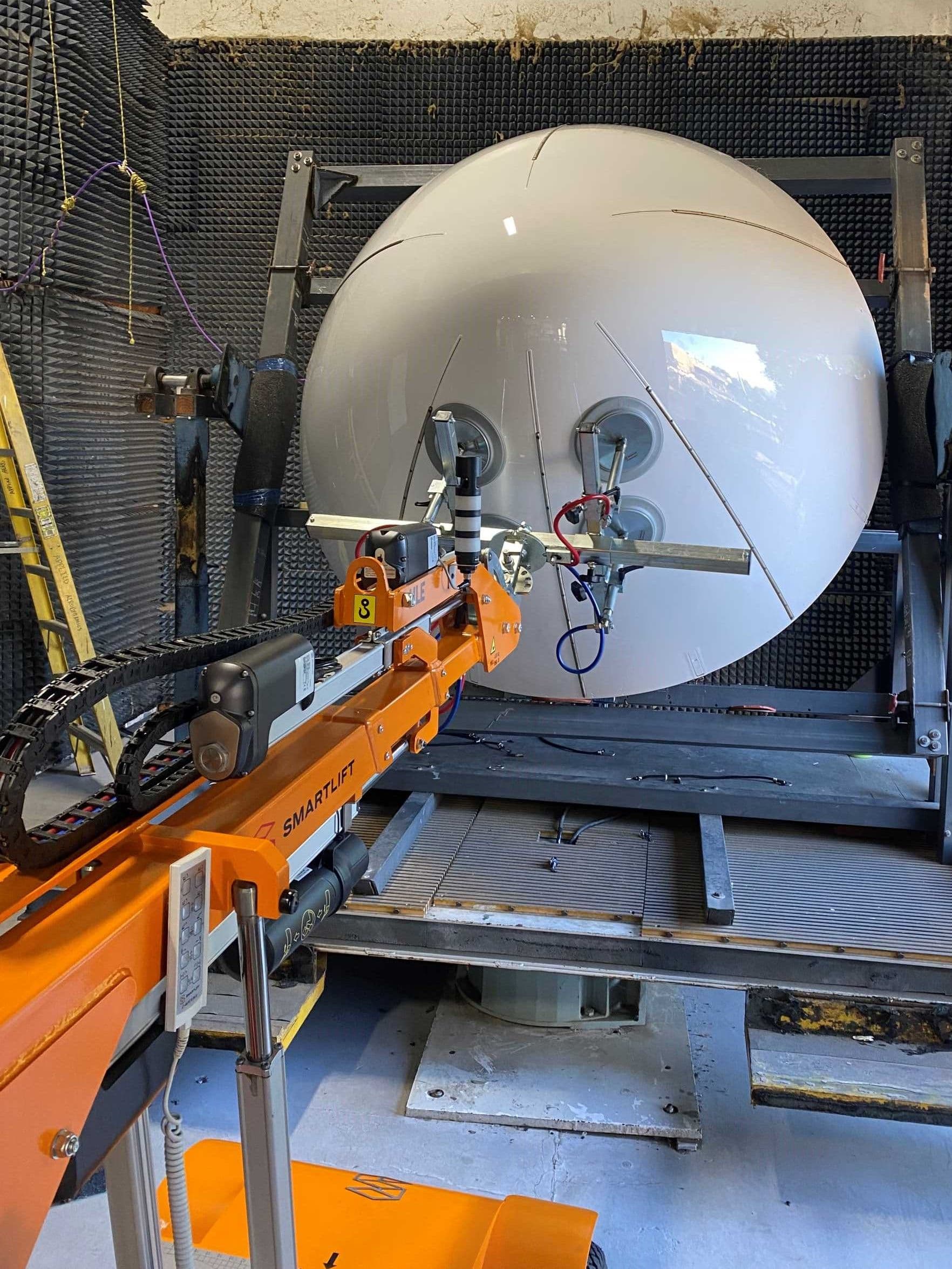
A strong helper for the heavy lifting
Aero FlightSystems wanted to find a solution that would relieve employees of the heavy lifting. They were about to buy a $150,000 crane when they contacted Smartlift to explore whether a vacuum lifter could help.
With the experts from Smartlift, they tested several suction cups on the SL 409 HLE RT, and they found the perfect setup for their needs.
The vacuum lifter SL 409 HLE RT is a lifting machine designed to handle tasks that require both extra lifting height and strength. The rotating yoke mounted on the lifter allows the team to place the nose of the aircraft on a rack in a perfect position in order to test the built-in radar equipment.
The lifter is easy to operate via a joystick, and with a lifting capacity of up to 950 lbs and a lifting height of 144 in, their SL 409 HLE RT easily handles the many heavy lifts without any physical strain on the employees.
Previously, eight employees were needed to handle the large aircraft components at Aero FlightSystems. With the Smartlift, two people can now do the same job, while the remaining six employees can focus on other tasks.
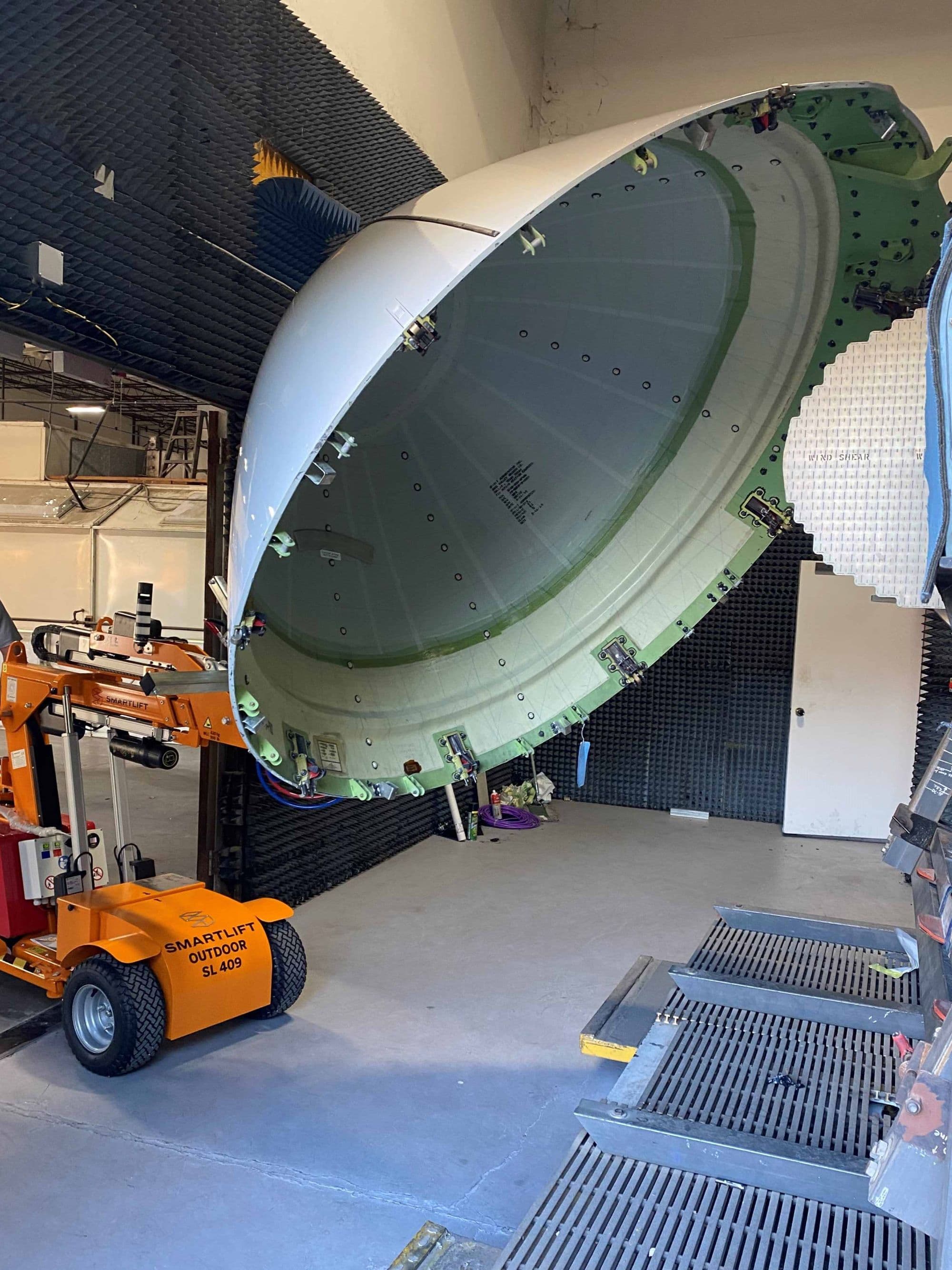
TALK TO ONE OF OUR EXPERTS
SEE THE vacuum LIFTER SL 409 HLE RT IN ACTION
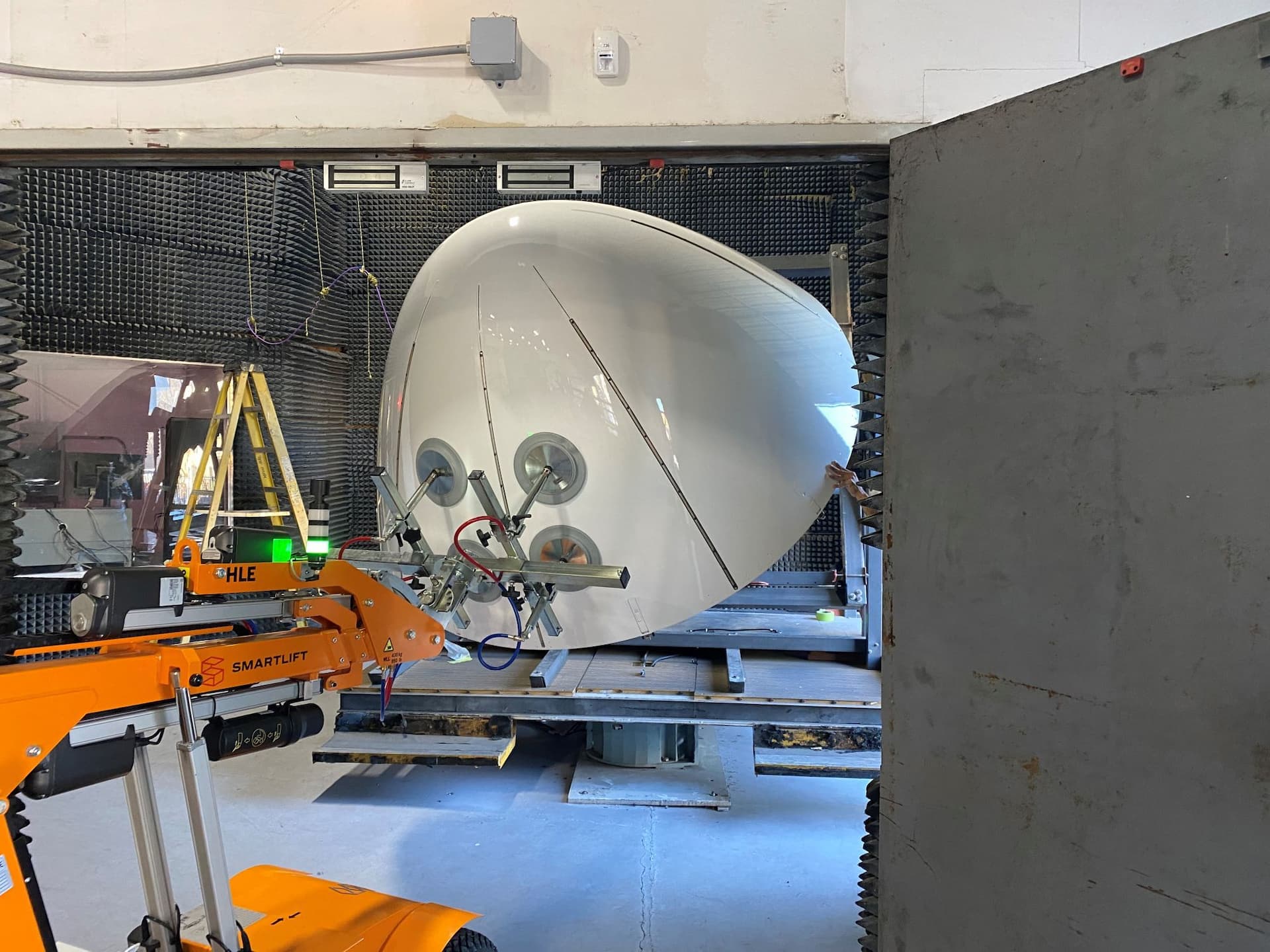
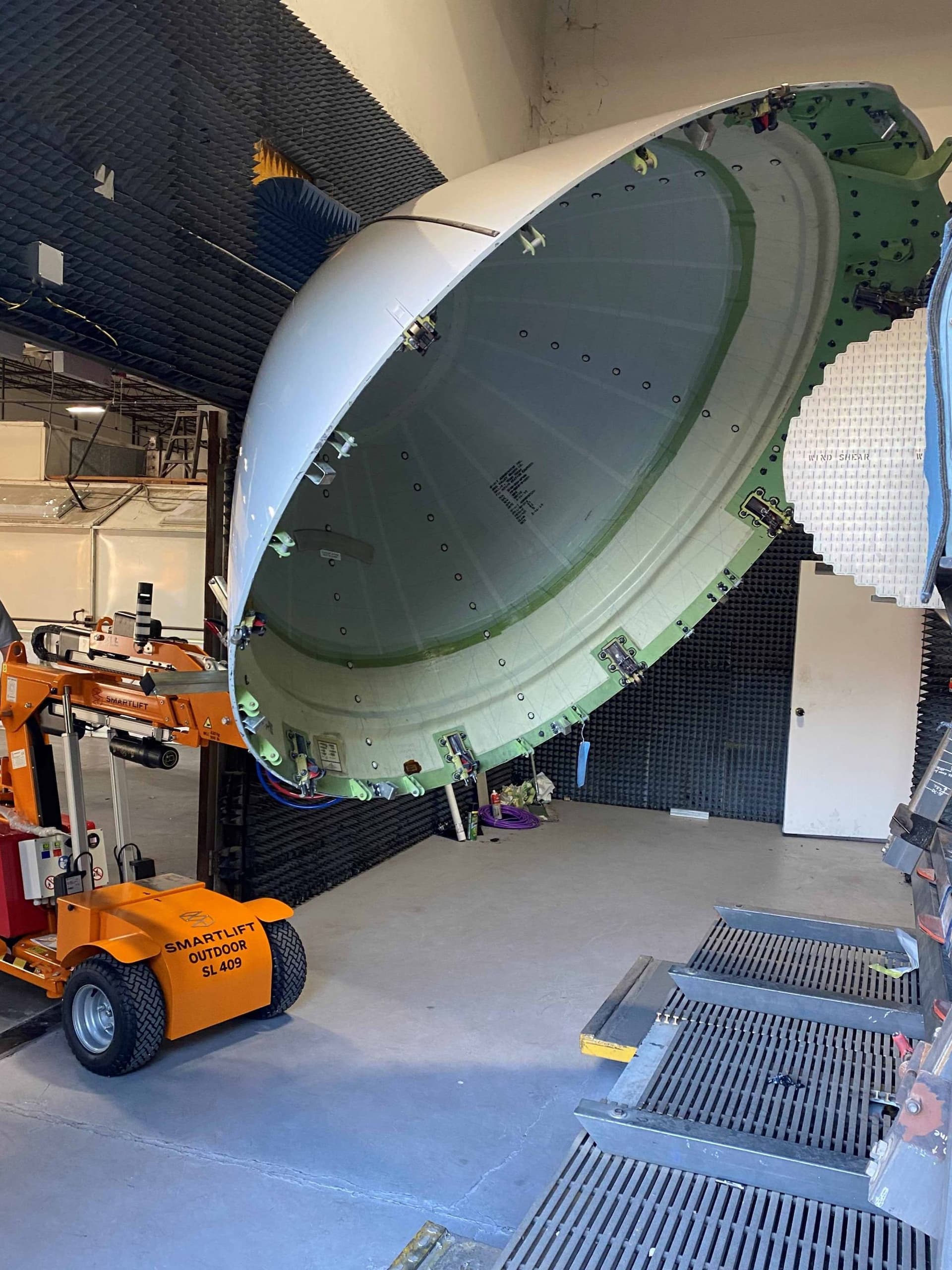
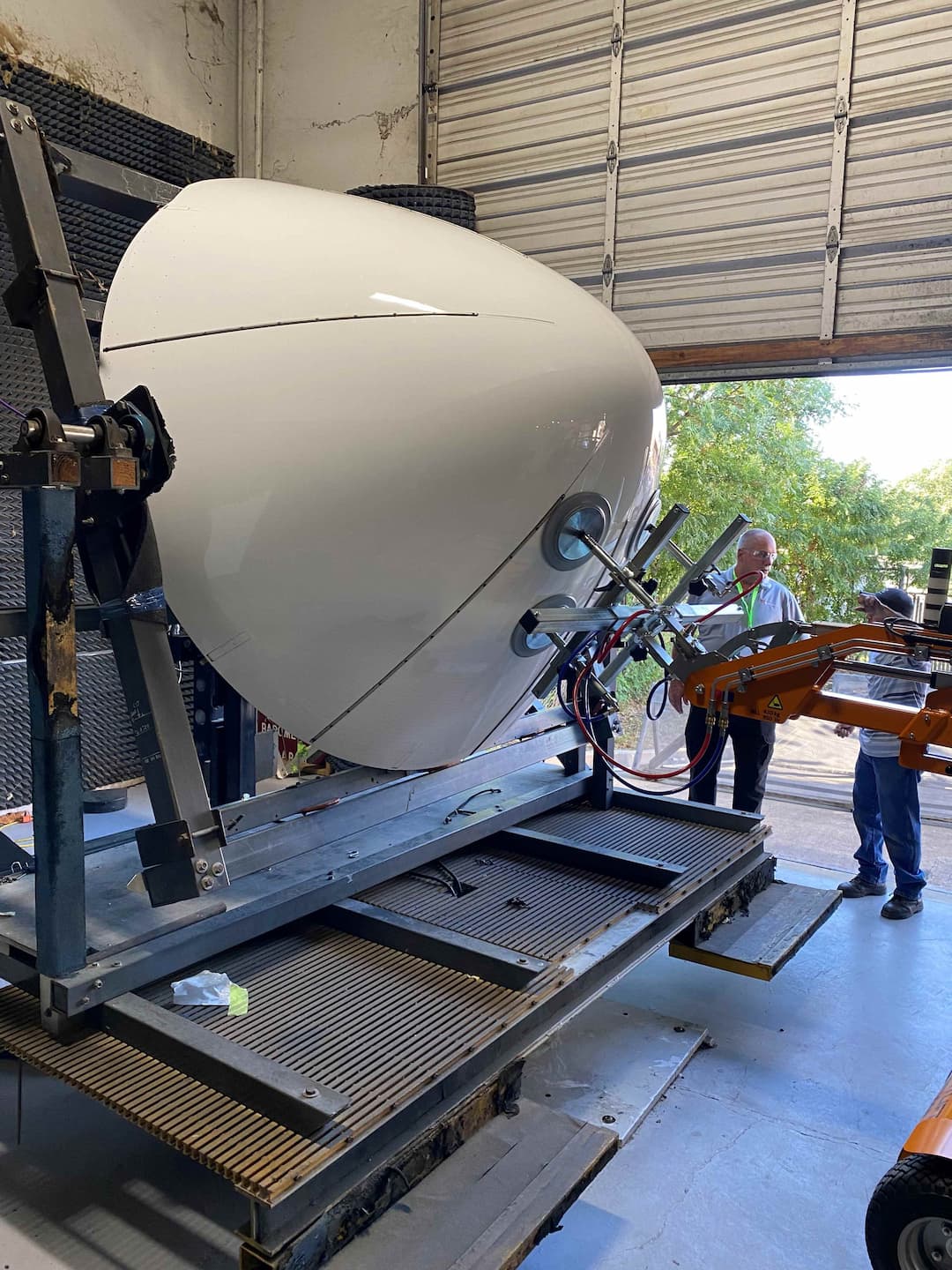
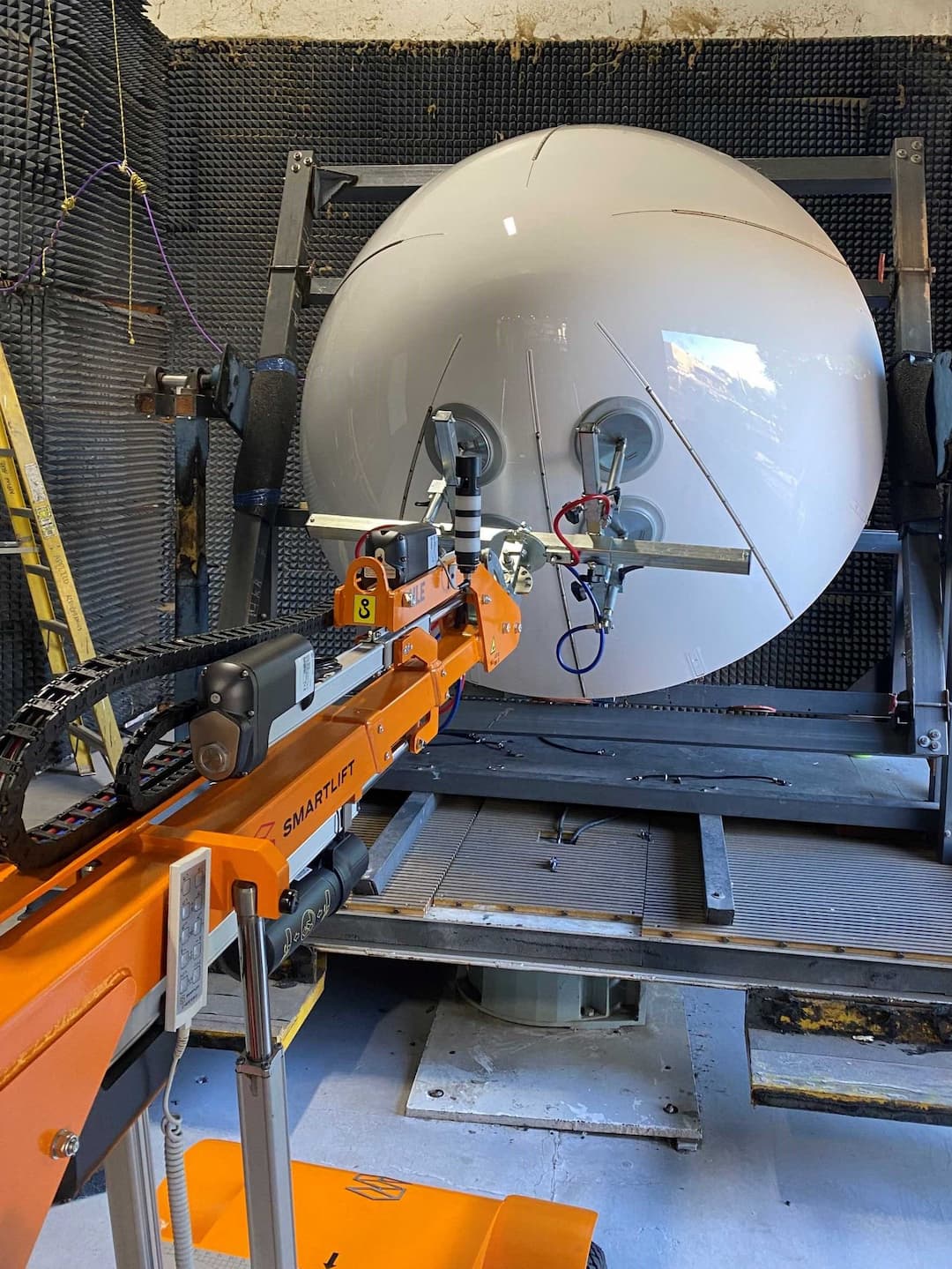
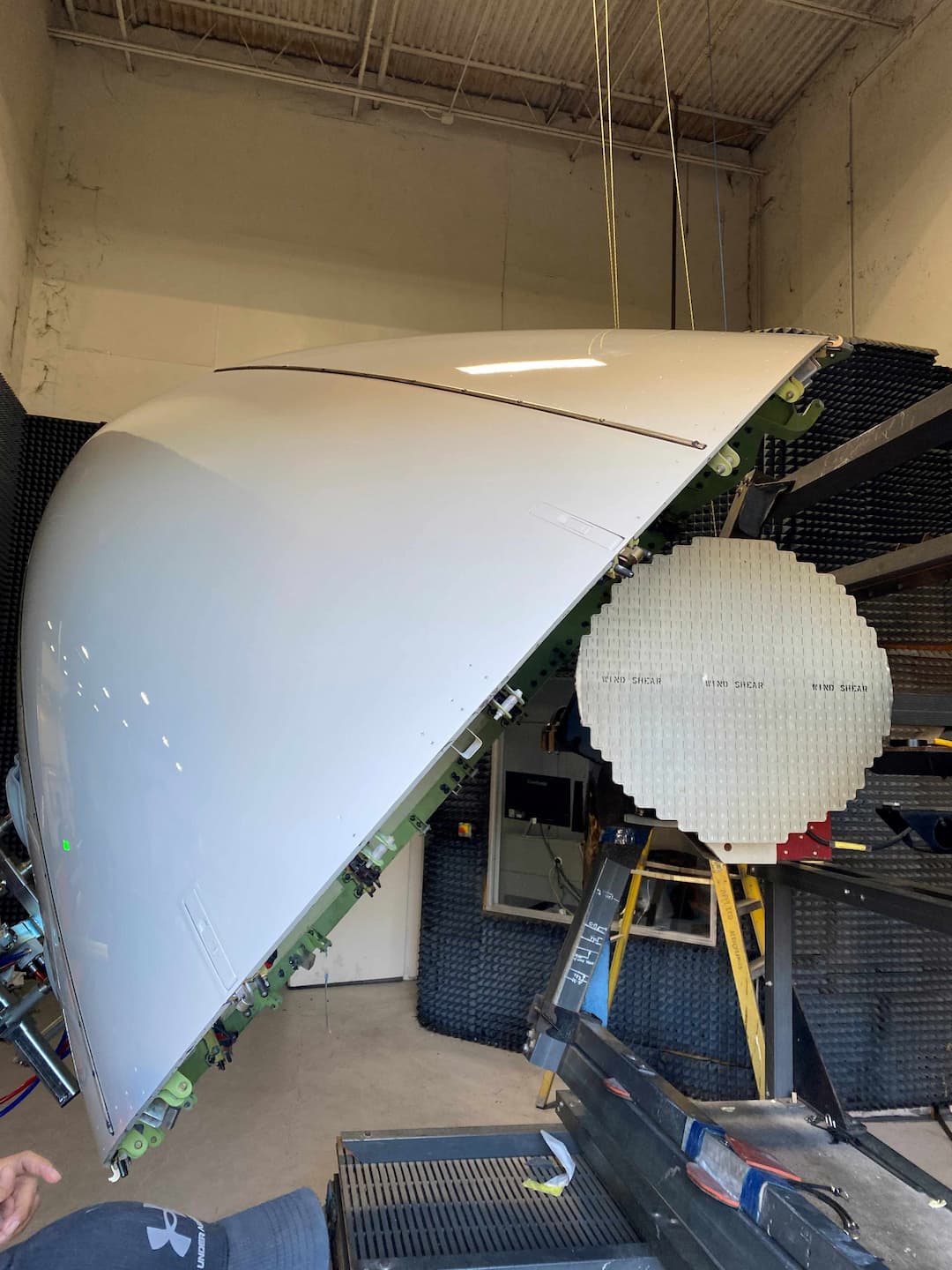